Plastic extrusion for tubing, profiles, and custom shapes
Plastic extrusion for tubing, profiles, and custom shapes
Blog Article
Checking Out the Different Strategies and Technologies Behind Plastic Extrusion
The world of plastic extrusion is a mix of technology, development, and precision, pivotal to numerous sectors worldwide - plastic extrusion. Advanced equipment, electronic controls, and a variety of materials converge in this complex procedure, creating top notch, sturdy items. As the market evolves, a change in the direction of sustainable materials and intelligent equipment is obvious. The complying with discussion will certainly clarify these strategies and innovations, while likewise hinting at the amazing future prospects of this vital production procedure.
Recognizing the Basics of Plastic Extrusion
The procedure of plastic extrusion, frequently hailed as a foundation in the world of manufacturing, forms the bedrock of this discussion. In essence, plastic extrusion is a high-volume production process in which raw plastic material is thawed and created into a constant account. It's an approach widely employed for creating products with a consistent cross-sectional profile, such as pipes, window frameworks, and weather stripping. The process starts with feeding plastic products, often in the type of pellets, right into a warmed barrel. There, it is heated and blended up until it comes to be molten. The molten plastic is then forced with a die, shaping it into the wanted kind as it hardens and cools.
The Duty of Various Materials in Plastic Extrusion
While plastic extrusion is a frequently used method in production, the products utilized in this procedure greatly influence its last result. Different types of plastics, such as pvc, abdominal muscle, and polyethylene, each offer distinct buildings to the end item. Manufacturers should very carefully take into consideration the homes of the product to maximize the extrusion procedure.
Techniques Used in the Plastic Extrusion Process
The plastic extrusion process includes different methods that are critical to its procedure and efficiency (plastic extrusion). The conversation will certainly start with a simplified explanation of the fundamentals of plastic extrusion. This will be adhered to by a breakdown of the process carefully and an exploration of techniques to boost the effectiveness of the extrusion method

Understanding Plastic Extrusion Basics
In the world of production, plastic extrusion stands as an essential process, crucial in the manufacturing of a wide variety of daily products. At its core, plastic extrusion involves transforming raw plastic material into a constant profiled shape. This is achieved by thawing the plastic, frequently in the kind of pellets or granules, and compeling it with a shaped die. The resulting product is a lengthy plastic piece, such as a pipe, cable, or panel coating, that keeps the form of the die. This cost-effective approach is extremely versatile, able to create complex forms and suit a wide range of plastic products. Basic understanding of these essentials enables for more exploration of the more complex facets of plastic extrusion.
Detailed Extrusion Process Failure
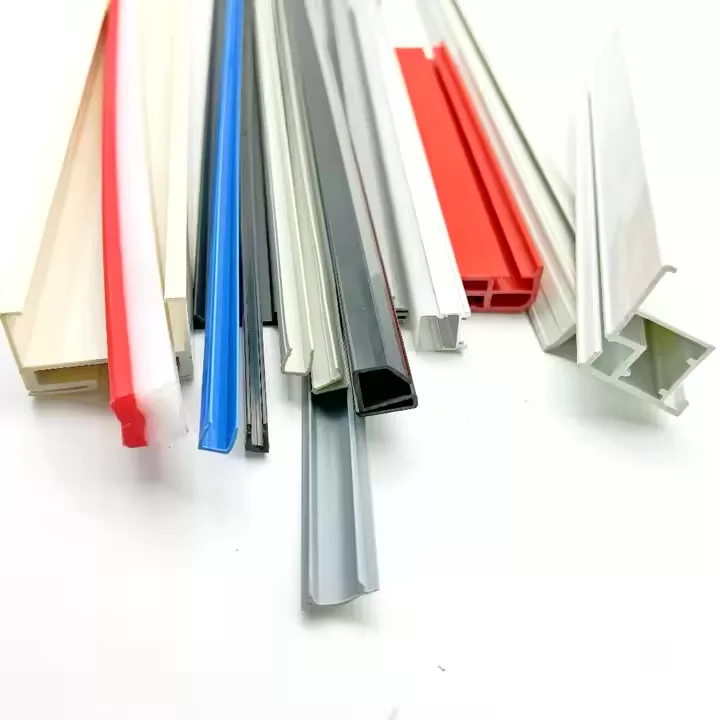
Improving Extrusion Method Efficiency
Performance gains in the plastic extrusion procedure can substantially affect both the quality of the last product and the total efficiency of the operation. Continual optimization of the extrusion method is vital to maintaining an affordable edge. Techniques that enhance performance commonly include precise control of temperature level and pressure throughout the procedure. Modern technologies, such as electronic systems and sensors, have contributed in accomplishing this control. The usage of top quality raw products can decrease waste and boost output high quality. Normal maintenance of extrusion devices can also decrease downtimes, therefore raising efficiency. Adopting lean manufacturing concepts can help get rid of unneeded actions in the procedure, promoting effectiveness gains.
Exactly How Innovation Is Altering the Face of Plastic Extrusion
The advent of new technology has considerably transformed the landscape of plastic extrusion. It has resulted in the growth of innovative extrusion equipment, which has actually boosted the performance and top quality visit our website of the plastic extrusion procedure. Moreover, innovations in the extrusion process have actually additionally been driven by technical improvements, using enhanced capacities and versatility.
Advanced Extrusion Equipment
Changing the world of plastic extrusion, advanced machinery imbued with sophisticated modern technology is ushering in a new era of performance and accuracy. These devices, outfitted with cutting-edge functions like self-regulating temperature level control systems, make sure optimal problems for plastic processing, consequently lessening waste and enhancing item high quality. High-speed extruders, as an example, magnify output rates, while twin-screw extruders offer exceptional mixing abilities, important for developing complicated plastic blends. In addition, digital control systems provide unprecedented precision in procedures, minimizing human mistake. These devices are made for durability, lowering downtime and upkeep costs. While these improvements are already exceptional, the continuous development of modern technology guarantees also greater jumps forward in the field of plastic extrusion equipment.
Developments in Extrusion Processes
Harnessing the power of modern-day technology, plastic extrusion procedures are going through a transformative transformation. With the development of 3D printing, the plastic extrusion landscape is likewise expanding right into new worlds of possibility. These technical innovations are not just improving the top quality of extruded plastic products but likewise moving the sector in the direction of a much more sustainable, effective, and innovative future.
Real-World Applications of Plastic Extrusion
Plastic extrusion, a functional and efficient procedure, finds use in plenty of real-world applications. The automotive official statement sector additionally utilizes this modern technology to produce parts like plastic and trim sheet. The toughness and flexibility of plastic extrusion, paired with its cost-effectiveness, make it an essential procedure throughout numerous sectors, underlining its widespread practical applications.
The Future of Plastic Extrusion: Predictions and Trends
As we look to the horizon, it ends up being clear that plastic extrusion is poised for considerable advancements and makeover. Environment-friendly choices to conventional plastic, such as bioplastics, are additionally expected to obtain traction. These patterns indicate a dynamic, developing future for plastic extrusion, driven by technical advancement and a commitment to sustainability.

Verdict
In verdict, plastic extrusion is an intricate procedure that makes use of innovative modern technology and differed products to develop varied items. As plastic manufacturing continues to develop, it stays a vital part of numerous industries worldwide.
In essence, plastic extrusion is a high-volume manufacturing procedure in which raw plastic product is thawed and developed into a continuous account.While plastic extrusion is a commonly used strategy in production, the products used in this process greatly affect its last outcome. At its core, plastic extrusion involves transforming raw plastic product right into a constant profiled shape. It has actually led to the advancement of sophisticated extrusion equipment, which has enhanced the performance and high quality of the plastic extrusion process.In final thought, plastic extrusion is an intricate process that makes use of sophisticated technology and differed products to create varied products.
Report this page